The Ultimate Metal Detection Solution Developed For A UK Food Manufacturer
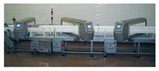

Click Here To Download:
The Guide To Reducing Metal Contamination In The Food Processing Industry
The Product Inspection Division has provided Rea Valley Speciality Foods with the most advanced metal detection solution for large product sizes yet to be installed by a UK food manufacturer.
Uncompromising standards
Dedicated to producing meats of the very highest quality, Rea Valley , who is specialty producer of the finest grade tongue products for both the delicatessen counter and pre-pack market, maintains a product inspection routine that far exceeds any existing industry standard. As part of this inspection regime, the company is committed to providing a product as free from metallic contamination as possible.
Highest levels of detection
Wishing to invest in a solution capable of successfully detecting the presence of minute metal particles and slithers of metal in frozen meat products weighing up to 25 kg, Rea Valley turned to METTLER TOLEDO Safeline to provide a solution that would not only offer the highest levels of metal detection, but would also accommodate such large product sizes.
Commented METTLER TOLEDO Product Inspection Division Business Manager, Mike Bradley: "Although we had not previously supplied product inspection technologies to Rea Valley , they were aware of our industry standing and have held several discussions with us over recent years. We were therefore delighted when invited to develop a ‘large pack' conveyorised metal detector for this high profile food manufacturer."
Before creating a metal detection solution for Rea Valley , the METTLER TOLEDO Safeline technical team first had to consider a number of key factors:
- Larger aperture capability
Firstly, in order to accommodate such large pack sizes, it was clear that a system with an extremely large aperture would be needed. Across the product inspection industry, it is widely accepted that the smaller the aperture, the greater the level of detection sensitivity. In developing their ‘R-Series Profile' range of metal detectors, however, METTLER TOLEDO Safeline have re-written the rule book, and offer unrivalled levels of sensitivity, performance, ease of use and reliability from machines with conveyor apertures of up to the size needed to inspect Rea Valleys products
- The orientation effect
Secondly, in order to provide the highest levels of metal detection, and to compensate for the ‘orientation effect', a state where a non-spherical particle of metal is easier to detect when passing in one orientation compared to another, it was decided that a solution containing three metal detectors – one straight and two angled at 40° would be required, as this would provide the very best opportunity of detecting as much metal contamination as possible, irrespective of its position (orientation), within each frozen block.
Trial unit supplied
Prior to building their full-sized solution, METTLER TOLEDO Safeline first supplied a trial unit to Rea Valley for exhaustive testing procedures. Delighted with the levels of sensitivity and detection provided, Rea Valley then commissioned METTLER TOLEDO Safeline to build a full-size conveyorised product handling, detection and rejection solution based around the proven technology offered by their Profile system.
Enhanced productivity
Concludes Mike Bradley: "Our solution has not only further improved metal detection levels for a customer who already works to the highest standards and views metal detection as an essential part of the production process, but has also enabled an increase in plant productivity by successfully accepting and testing larger pack sizes. In creating this new triple head solution, we have developed a new industry benchmark for those organisations requiring the ultimate levels of metal detection.
The Guide To Reducing Metal Contamination In The Food Processing Industry
SOURCE: Mettler-Toledo Product Inspection