Factors To Consider When Selecting A Conveyor Belt In The Snack Food Processing Industry
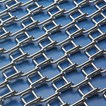
As a society that undoubtedly enjoys its savory-salty snacks and confectionary diversions, we have made the snack food business a multi-billion dollar industry. Even with new emphasis on health food and healthy snacking, the snack food industry as a whole is still growing. Because of this trend, there has been a significant increase in the demand for processing equipment.
Conveyor belts are used to transport these foods through the various stages of production. Each type of conveyor belt offers different advantages and performance characteristics. While metal belts are primarily used in baking, frying and cooling operations more than any other types of belts, there are still many snack food companies that prefer the plastic variety in many stages of the production process. In fact, until plastic belts arrived, metals belts were far more prevalent throughout food manufacturing; now plastic and metals belts are used side by side in many of these snack-food operations.
Of the metal belts, the most popular are stainless steel belts, which do not sweat, slip, or droop, although some, like those used in many confectionery applications, are also constructed of carbon steel music wire. Plastic modular belts are usually assembled from injection-molded plastic parts and can be constructed from a wide spectrum of materials, including polystyrene, polypropylene, polyethylene, polyurethane, polyvinylchloride, and nylon. Other belts may be constructed of various types of woven fibers, like canvas or nylon filament, and covered with vulcanized compounds such as rubber or vinyl.
If you are a snack-food manufacturer looking to optimize production, reduce downtime, and keep costs down, how do you decide which belt to choose for your operation? It's a procedure that must be given careful consideration; some helpful guidelines to lead you through the decision-making process include:
FDA regulations. The advantages of metal are not subjective; empirical data collected over a period of time highlights them very clearly. One of the thorniest issues in the food packaging industry – snack foods included - is the prevalence of "extraneous material inclusion." Data available through the Food and Drug Administration (FDA) and the United States Department of Agriculture's (USDA's) Food Safety Inspection Service reveals that of all the extraneous material inclusion found in packaged food products, the vast majority is plastic. This, of course, does not mean that all of it traces back to the conveyor belts, but it certainly is safe to assume that the belt would probably account for some percentage of the total.
Cleanliness. A second concern regarding belts – although no less crucial – is the area of cleanliness. Because plastic belts are modular in construction with the individual components injection molded, they require hinge pins, through rods, and link barrels for assembly. Conversely, metal belts, particularly stainless steel, are, in many cases, hinge-free, easier to clean (as their openness allows flow-through not only of heat but of the chemicals and solutions used in the cleaning process), and offer no place for bacteria to hide. And given that the surface of a plastic belt can become scratched during cleaning cycles far more easily than stainless steel surfaces, they may then contain surface crevices or topography patterns. These not only become places for allergens and pathogens to hide, but depending on the process, could also promote bio-film contamination and buildup over time.
Even some types of metal conveyor belting can raise issues of cleanliness. Balance weave metal belts are prevalent in the snack food industry, notably in baking and frying operations, but they do carry some downsides. Because balance weave belts consist of a two-layer metal spiral or helix process with through-rods, they are also more difficult to clean.
Allergens. The importance of the allergen issue cannot be overstated. The advantages of stainless steel are so numerous that in its report, "Guidance on Inspection of Firms Producing Food Products Susceptible to Contamination with Allergenic Ingredients," the Office of Regulatory Affairs for the FDA specifically cites stainless steel as its prime example of a material that can be easily cleaned. Since it is estimated that upwards of 4 million people in the United States have true food allergies, and considering that the medical consequences of a food allergy can be quite severe – as can the financial ramifications to the food manufacturer – this is not a concern to be taken lightly.
Safety. In evaluating the characteristics of the different materials, it is hard to ignore one of metal's most distinct advantages: if a tiny piece of the belt breaks off, the standard metal-detecting equipment that is normally a fixture in any food processing operation will discover it, significantly decreasing the possibility that the fragment will find its way into the finished product. If a piece of plastic breaks off, however, it can more easily slip through.
Fire safety is also a top priority. There have been a fair number of instances of fires with plastic conveyor belts in tortilla and other snack food operations, particularly at the juncture of the oven or fryer and the cooling conveyor. The chances of a stainless steel belt catching fire on a cooling line – or any part of the manufacturing operations – are essentially zero.
Tight grid. A tight grid that helps ensure that product does not fall through or get pushed out through the carrying surface is critical. There are now belts offering as much as 70% open surface area while maintaining a mesh design small enough for snack food applications. Such a combination provides optimal performance in product coating, drainage, and liquid or air circulation, as well as significantly facilitating the cleaning process.
Cooling. The advantages of metal become especially noticeable in cooling operations. Plastic is an insulator, meaning that it will absorb and retain a great deal of the heat from any product coming out of an oven onto a cooling conveyor. Stainless steel, on the other hand, conducts heat, and thus will dissipate it into the surrounding air. As a result, cooling is a far less time-consuming process.
Energy efficiency. Some stainless steel belts are far more open and provide better flow-through or convection characteristics than plastic, so that the efficiency of the cooling process is further improved, saving valuable energy and the associated costs. Among metal belts, balance weave conveyor belting lacks the convection characteristics of a more open mesh belt because of its double layer wire helix construction.
Weight. Compounding the problem is that many of these belts are not only chain-driven but are very heavy, meaning that they will suck up a great deal of energy through heat absorption, as well as electricity because of higher horsepower requirements. Obviously it is best to find belts that are as light as possible – much lighter than balance weave belts – to keep horsepower requirements, and energy consumption, as low as possible.
Cost stability. Not to be forgotten is that most plastics are petroleum-based products; consequently, their cost is inexorably linked to the cost of oil. With the recent increases in the cost of a barrel of oil – and further increases always on the horizon - the cost of plastic belts is a consideration that should not be overlooked.
Armed with the knowledge that metal belts have well-defined advantages over plastic belts in a snack-food operation – and that even among metals belts, the more open mesh stainless steel belts can prove superior – the search for the appropriate metal belt should be easier. Ultimately, it is best to locate a belt that is engineered specifically to handle smaller, more delicate products, while providing a lighter weight, open-mesh belt design. In addition, a belt that provides strong product support, excellent flow-through, and competitive cost is also an advantage.
Clearly, the arrival of these superior, highly functional belts comes at an encouraging time for the snack food industry. Based on the public's massive consumption of these tasty treats, the industry is clearly experiencing a boom that is projected to continue for some time. And open mesh stainless steel belting will play a crucial role in ensuring that the way those snacks are prepared is efficient, safe, and cost-effective.
SOURCE: Wire Belt Company of America